HOW TO HACK A DRILLMOTOR
(Based on a Chicago Electric Drill)
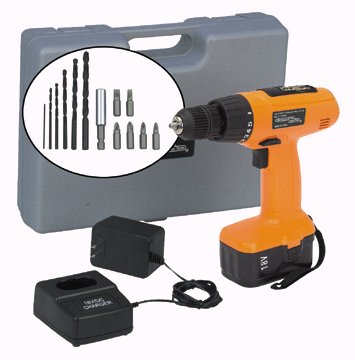
This article describes the steps in removing and modifying a motor and
gearbox from an inexpensive cordless drill. The one we are using as an example is
a Chinese manufactured Chicago Electric 18V 3/8" chuck drill, item number 44849, which are available from
Harbor Freight Tools .
These drills are listed at $69.99 but are always on sale for $39.99.
The motor and planetary gearbox inside them will run at 900 RPM at 18V and
produce about 100 oz-in of torque. Do a search for cordless drill
or use the item number search to find these.
Ted Zeiger, of Team Cosmos, first turned me on to these motors when I was first getting started,
but I was concentrating on bigger iron at the time. At had bought 8 of these things, but never got
around to using them, until BotBash 2002 came around. I'm slowly moving to lighter bots now and Ted, who
is a
champion 'little' bot builder, told me how to hack these drills. I've experimented with other models now, and
all cordless drills
seem to be built the about same way, so the procedure
described here may be applied to other types as well.
Step-by-Step
|
Brand new, out-of-the-box! Leave the battery pack on for now. It has a slight
charge which we are going to need in a couple of steps
|
|
First, open the chuck as wide as it can go. Look inside the chuck. You'll see
the head of a screw in the center. It may be a cross-head or straight-slot. Use
the appropriate driver and loosen the screw CLOCKWISE while grasping the chuck
body. This is a left-hand thread scre, used so it won't loosen during normal
drilling.
|
|
Drop the screw out and carefully set it aside. You DO NOT want to lose this
screw! You will not find them at hardware stores.
|
|
Here's where we are going to use that battery power. Adjust the direction of the
drill so that it will spin in reverse, opposite the way you would normally drill
holes. Put it in the drill mode, not one of the clutched driver settings.
Holding the chuck firmly (you little guys should hold the chuck in a vise or
with vise-grips), turn on the drill and the chuck should immediately break free
and unthread itself from the motor spindle, exposing the male threads.
|
|
The threads on these motors are 3/8-24UNF. although the larger drill motors use
1/2 inch diameter threads.
|
|
Take the screws off the clutch spring retainer plate. The springs underneath
will force this up toward your driver. keep this plate for later. You might want
this for mounting your motors in the bot.
|
|
Remove the clutch housing, spring and shims. Keep the metal parts, except got
the compression spring.
|
|
Ball bearings are used to put force on the clutch. There are two in series in 8
or 6 pockets. In some motors they will fall out toward the front, others
only come out when you disassemble the transmission.
|
|
Remove the plastite screws holding the drill body together and separate the two
halves. put these screws in your hardware cache, as you may need them for other
things (building antweight bots!)
|
|
Now you are down to extracting your coveted motor and transmission.
|
|
Cut or yank the wires away from the switch assembly and discard the switch and
heatsink.
|
|
These are the parts, along with the motor, that you may want to keep. There are
many ways of mounting these in a chassis. I'll show you one way in an upcoming
step.
|
|
Take the three screws the hold the motor to the transmission.
|
|
Hold the motor in your hand so the threaded end is vertical and jiggle the
transmission until it comes free. Hopefully you will leave the outside
cylindrical clutch piece with the motor and all of its assorted planetary
gears.
|
|
Depending on the size of your motor, run a tap through four or three of
the empty ball bearing pockets. For this motor we are putting 10-32UNF threads
in four of eight pockets. Ted Zeiger prefers 10-24UNC threads, but either one
works as well. We are going to be putting set screws in these holes in a couple
of steps. In a larger motor, with a two speed transmission, The ball bearing
pockets were large enough to use 1/4-20UNC tap (or 1/4-28UNF).
Keep the tap parallel with the transmission shaft and look on the far side,
while turning your tap, so you don't go too far and start tapping part of the
shaft hub.
|
|
On the inside, when you are done tapping, use a small wire or driver and pick
out the plastic curls that were created when you were tapping the plastic.
You'll notice three (or four) small shafts sticking out of the hub. These have
to fit into their corresponding spur gears. If you can re-assemble the
transmission body back over the transmission pieces, do that now. If you think
you may not have put them in the right place, just simply pull them out of
transmission and place them over the shaft and move all the transmission parts
over to the transmission housing. Its fairly easy, once you see how it works.
|
|
Now you've got all the parts over to the transmission, pull the motor end off.
|
|
You'll see two screws (I wish there were more) which hold the motor to the
transmission mounting plate. Tighten these screws, as
sometimes they come loose. After some use, and if the motors aren't supported
well, these screws loosen up, which means you will have to re-tighten them in
between matches. Try putting some Loctite on them at this time.
Replace the motor into the transmission housing being careful to match up the
keys that orient the two units. And put the plastite screws back in that hold
the assembly together. Some motors do not have screws and rely on the drill
motor housing to hold everything together. You'll have to make up some structure
in your chassis to keep the motor and transmission from separating.
|
|
Now that the motor and transmission are together again, rotate the threaded
shaft so that the protrusions on the transmission cylindrical clutch are not
directly under your tapped holes. Using a hex wrench, install your set screws
in all your holes. Try 5/16 long set screws, they need to be flush when you are done.
When you think you have bottomed out your set screws evenly, try
rotating the threaded shaft back and forth to see how much play you have.
You want to eliminate the play but you don't want the screws actually pressing
on anything as it puts a strain on the plastite screws holding the motor and
transmission together.
|
|
You may want to skip this step, but in Wedgward-Ho's design I needed to remove the
two bosses at the business end of the transmission, and use shorter plastite screws to mount the motor.
|
|
Here's the hacked motor all ready for installation in your bot.
|
|
This is everything you can throw away, now, unless you want to keep the
batteries and charger. Don't keep the drill bits and accessories that came with
these drills as they are or really poor quality and will break or get dull as
soon as you use them.
|
|
You can use the charger and batteries as they come with the set, if you have
room for the size of the battery pack. I went ahead and tore the battery pack
apart and taped all the batteries together. There were two that were separate
from the others. so I wired them in series after cutting them from the main
pack.
|
|
Here's a not-so-pretty, but usable 18V battery pack. The batteries only charged
up to 1.2 Amp-Hrs, unlike the 18V Battlepacks from Steve Hill, which went to 3
Amp-hrs. So, if your bot runs long enough on a charge, you may be able to use
the ones that come with the drills. Keep in mind, you may be using 2, 4 or 6
drill motors in your bot, so if you can afford the weight, put all the battery
packs in parallel. You should have enough for even the longest fights.
|
Mounting Techniques and Tips
|
There are two flats on the end of the motor that can be used for keeping the
transmission from turning when the motor is spinning.
|
|
The double-D shape of the transmission end is about .135" in diameter. I
use a step drill that goes up to 1.125 and it seems the hole is a slight press
fit (the plastic gives way). The tubing shown here is .75 X 1.5 .049 wall 4130
chromoly steel.
|
|
Here I've welded the chrome piece that came with the drill, that has a Doulble-D
shape to act as an anti-rotation key for the motor.
|
|
Here's the motor slipped into the chassis.
|
|
I then followed up with the clutch spring retainer plate to keep the motor in
place. I have now changed my method and weld this plate in place. For the
double-D key I weld two staps in the 1.125 hole so that it better supports the
motor.
|
|
Here is Wedgeward-Ho in the rough, prior to adding the weapon motor and
painting.
|
|
Here is Me-Me, shown with a two speed transmission motor. The significance here
is that there are no screws tying the motor and transmission together so it was
necessary to use hose clamps to hold the motor in a cradle that was welded onto
the chassis. The transmission screwed onto the clutch spring mounting plate
which was welded to the chassis, using the original plastite screws.
You'll also notice that there are #25 sprockets pressed into the wheels that are
then mounted directly to the motors.
|
|
Here's the weapon motor for Wedgeward-Ho held against a spacer with a hose
clamp. You really need to do this with your drive motors as well. It will keep
the motor from coming apart on you and saving you a tremendous amount of trouble
at a competition.
|
|
Colson hubs can be modified by making an aluminum hub which will press into the
wheels. The I.D. of the hub has been drilled with a 'Q' size drill and tapped
with a 3/8-24UNF thread. You can also attach a #25 chain type-B sprocket
directly to the drill motor by drilling and tapping the sprocket accordingly.
|
|
Screw the wheel and hub assembly onto the drill motor shaft, but do not use
Loctite here. The shaft is very soft steel...
|
|
Add Loctite to the lefthand screw that used to hold down the drill chuck...
|
|
...put a 1/4 I.D. washer over the screw and install into the wheel hub by
rotating counter-clockwise.
|
|
Final note: If you can afford it, the premium system, using American made Dewalt drill motors,
is available from Team Delta.
Dan Danknick will supply you with custom hubs, as well as Colson wheels.
|
Copyright © 2001-2002 Mike Konshak. All Rights Reserved.